space frame Production Process
Production and manufacturing process of space frame member and quality control
The main parts of the space frame project is bolt ball, member, the sleeve, sealing plate, cone, bearing, bracket.
(A), manufacturing production order and schedule
The production schedule of steel components manufacturing and construction schedule table (see the attached table).
(B) manufacturing of bolt ball
1 Production process of bolt ball: 45 # round steel by forging →fabrication hole processing →number → webs and chords screw processing → painting → packaging.
2 The round steel fabrication will under Saw cutting material. The relative height H / D of the Blank is from 2 to 2.5, it is not allowed gas cutting.
3 Forging ball blanks are using loose tooling forging. The forging temperature from 1200 ℃ to 1150 ℃ under the insulation. The temperature should be on average and the end-stage temperature should not lower than 850 ℃. The forging equipment will us air hammer or press. After forging, it will be normalizing naturally in the air.
4 screw holes and flat processing should be carried out following the process: split plane → tap drilling→orifice chamfering → tap tapping thread.
5 screw holes fabrication with special tooling machining lathe, screw holes with a setup machining plane.
6 Print Ball number, work number in the machining process bore plane.
7.The main testing control of the bolt ball are:
a burnt, crack; with a magnifying glass and control injuries UT inspection. b bolt quality: 6H level should be achieved ,using standard thread gauge test.
c. Ball screw mild and bolt ball intensity: the use of high-strength bolts with a tensile testing machine, according to a group of 600, each batch will take 3.
d. it allows you to check the deviation of the project. Test criteria are as follows;
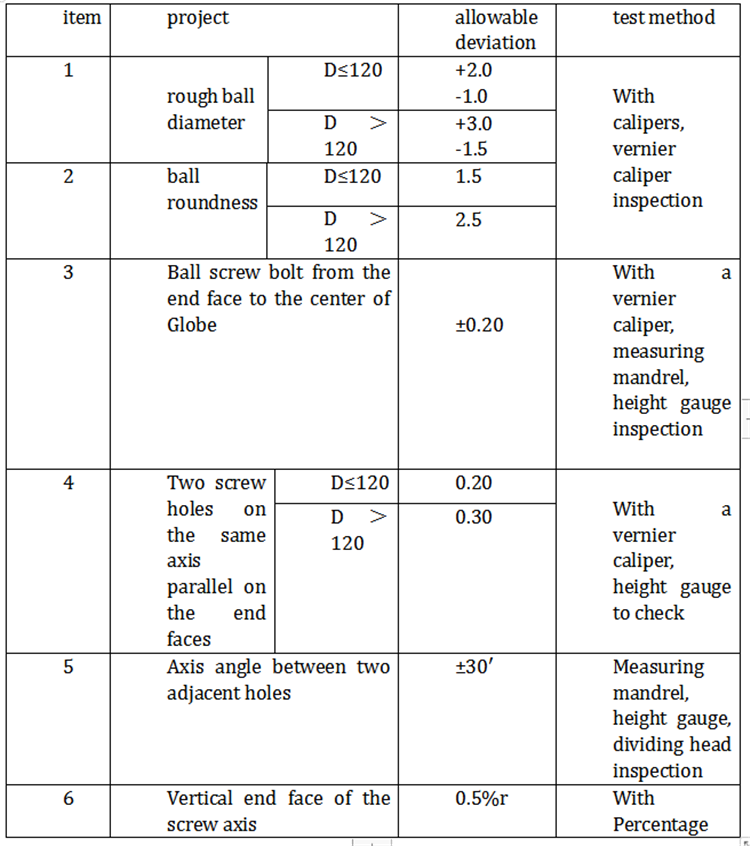
(C), the member production
1.the member is consisted from the pipe, sealing plate or cone and high-strength bolts, whose main process are: pipe cutting and beveling number → pipe and seal plate or cone, supporting high-strength bolts and spot welding → automatic or semi-automatic carbon dioxide gas welding (grade 2 welds) → shot blasting (Sa2.5 level) → painting → packaging.
2 pipe cutting and beveling will be used by pipe cutting machine one time.
3 Bar assembly welding: weld the steel tube, hammer, shrouding and high strength bolts by mould according to the double sample drawing.
4 Bars are welded by CO2 protected welding or handmade electric-arc welding.
5 The welding rod between bars, hammer and shrouding is E4303 while the welding stick is H08Mn2siA.
6 The bar welding should be in accordance with GB50205-95and JGJ81-91< steel structure construction welding regulation>.
7 The main inspection controlling of bars are in following:
The groove of bars and the length of groove after the bar must reach ±1mm.
Number and flaw detect the quality of welding joint by ultrasonic, spot check 30%.
The intensity of destructive testing of welding joint by tension tester, spot check 3pcs in each 300pcs.
Coating quality:
the environment temperature of coating should be >5℃,the humidity<80%.
It’s controlled by hygrothermograph and tested by thickness tester, the thickness should be 25um±5 each time.
Testing of allowable deviation:
Length: allowable deviation±1mm.
Axis straightness: allowable deviation L/1000,and ≤5mm.
Bar left end face and axis perpendicularity: allowable deviation is 0.5% of end face radius.
Bar steel pipe should be bundled for easier transportation, stack and storage.
Ⅳ、Production of shrouding, hammer and sleeve
Production of shrouding
The shrouding is processed by following procedure:
round steel blanking →machining.
Shrouding is blanked by sawing machine.
It’s processed on lathe according to shrouding standard drawing.
Production of hammer
The hammer is processed by following procedure:
round steel blanking →moulding bed forging workblank→normalization→machining.
Round steel is blanked by sawing machine.
Hammer forges workblank by press machine. The forging environment should be kept between 1200℃and 1150℃, the finish forging temperature should not lower than 850℃, and naturally normalized after forging in the air.
It’s processed on lathe according to hammer standard drawing.
UT inspection.
Production of sleeve
The sleeve is processed by following procedure:
round steel blanking →moulding bed forging workblank→normalization→machining→ first treatment of corrision prevetion(descaling).
Round steel is blanked by sawing machine.
Round steel forges workblank by press machine. The forging environment should be kept between 1200℃and 1150℃ and uniform, the finish forging temperature should not lower than 850℃, and natural normalized after forging in the air.
It’s processed on lathe according to sleeve standard drawing.
It’s treated of descaling by design requirements.
The main inspection controlling contents of shrouding, hammer and sleeve are in followings:
The apparent defects of overburning, flaw,scale cinder and etc, spot check 10% quantity by magnifying glass.
Pressure bearing test 5‰sleeves, intension test the shrouding or hammer matched up with bars.
Allowable deviation item inspection
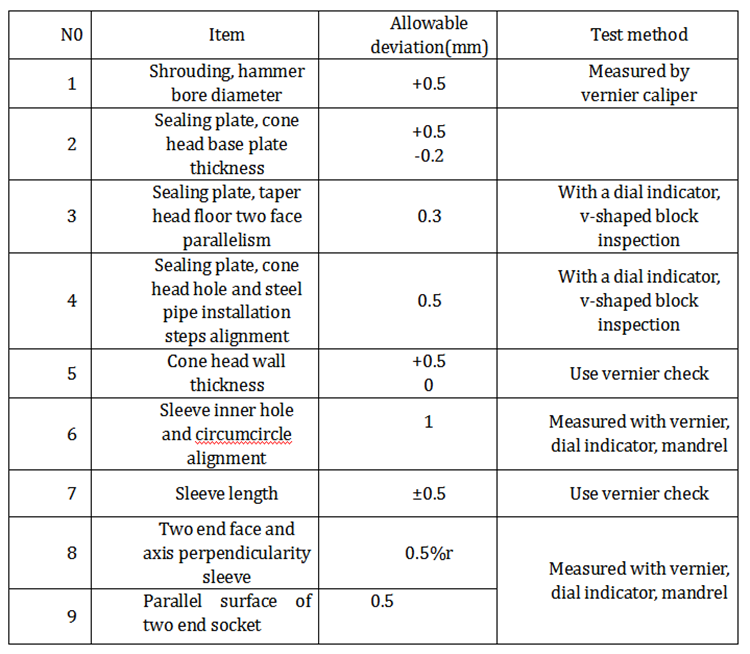
(Ⅴ) Support production:
Support processing according to the following process: support rib plate and bottom plate blanking→support bottom plate drilling→support rib plate and bottom plate,rib plate and rib plate, rid plate welding with the ball→anti-corrosion pre-treatment (cleaning)→anticorrosion treatment (coating).
Support rib plate and bottom plate blanking with gas cutting.
Support bottom plate processing adopts the radial drilling machine.
Rid plate and bottom plate、rid plate and rid plate CO2 gas shielded welding with welding and manual arc welding,welding material is welding wire:HO8Mn2SiA,welding rod E4303.rid plate and bolt ball welding using manual arc welding, using E5016 electrode welding, preheating before welding processing, then layered welding, requirements of weld heat preservation slow cooling.
According to the design requirements for the anti-corrosion pre-treatment and anticorrosive processing.
(Ⅵ)Bracket production:
(1)Bracket processing according to the following process: bracket pipe and the plate blanking,→welding.
(2)Bracket pipe blanking using the pipe cutting machine.
(3) Bracket pipe and the plate connection using E4303 manual electric arc welding.
(4) According to the design requirements for the anti-corrosion pre-treatment and anticorrosive processing.
(Ⅶ)Main seal plate, cone head, the sleeve inspection control contents are as follows:
Support,bracket are in the ball is processed on the basis of production processing, its main process is: steel plate cutting→steel plate between the base or bracket welding→with the ball welding→ surface treatment→packing, the main content of the test :
The welding between the steel plate: all for fillet weld, weld quality should reach level 3 above, weld height should meet the design requirements and regulations.
With the welding of the ball: the E50 series welding rod, welding quality should reach level 3 above, the weld height must meet the design requirements.
Of the base plate flatness should be not more than 3 mm.
Bore bolt ball chord (or web member) and the angle of the base plate or plate position error should be not more than ±20’
Bolt ball center and bearing plate offset should be not more than ± 5 mm
Space frame parts processing to try to assemble conditions, should try to assemble in our factory, try this project space frame area of not less than 300 m2,try to spell space frame should only after acceptance by the quality control department must remove the packaging. Try to assemble before inspection network frame parts shall not be outbound.